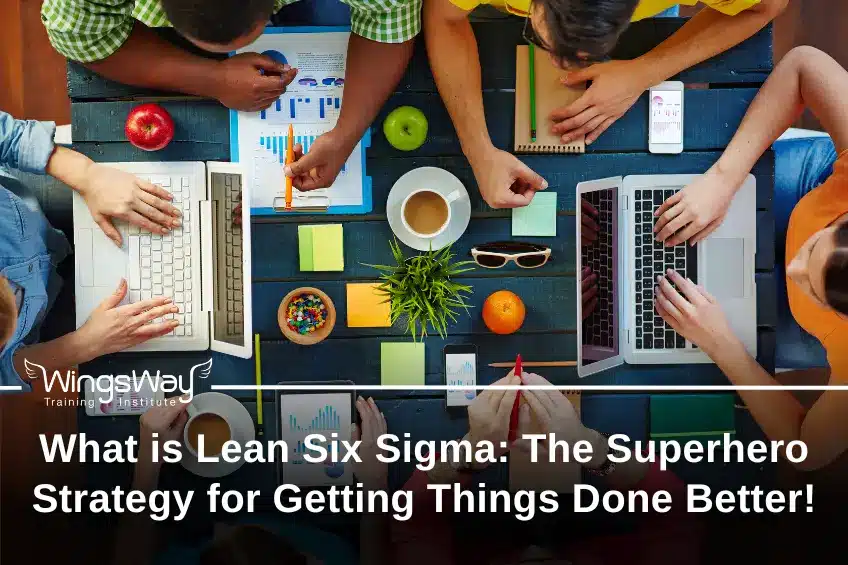
What is Lean Six Sigma: The Superhero Strategy for Getting Things Done Better!
In a world where efficiency defines success, Lean Six Sigma (LSS) has emerged as a cornerstone of operational excellence. Whether you’re a business leader looking to streamline processes, an employee wanting to stand out at work, or a freelancer seeking smarter workflows, understanding LSS can be a game-changer for everyone.
But what exactly is Lean Six Sigma, and why is it considered essential today?
This comprehensive guide dives into the concept, methodologies, and real-world applications of Lean Six Sigma and gives you tips on how you can use it personally or professionally to improve the way you do your everyday tasks.
What is Lean Six Sigma?
To understand Lean Six Sigma, it helps to break it down into two parts: Lean and Six Sigma — each powerful on its own, but unstoppable together.
Lean is all about speed and simplicity. It focuses on cutting out anything that doesn’t add value, like wasted time, unnecessary steps, or unused resources. Think of it as the “decluttering” expert of business processes.
Six Sigma, on the other hand, is all about precision and consistency. It uses data and statistics to identify and eliminate errors or defects, ensuring everything runs smoothly and delivers high quality—every single time.
Now, combine the two and you get Lean Six Sigma—a results-driven methodology that helps businesses streamline their processes, eliminate waste, reduce errors, and deliver better outcomes for customers.
So what does that look like in real life?
Imagine you’re running a lemonade stand. Lean Six Sigma would help you:
- Avoid spilling juice or wasting lemons – that’s Lean, helping you minimise waste and save resources.
- Make every glass of lemonade taste exactly the same–that’s Six Sigma, making sure your product is consistent and high quality.
Now imagine doing that faster, cheaper, and with happier customers.
That’s the power of Lean Six Sigma.
The Concept of Lean Six Sigma
Lean Six Sigma combines two ideas:
Lean focuses on getting rid of waste. It’s like cleaning out your toy box; keeping only what you actually play with and removing everything else that just gets in the way.
Six Sigma focuses on making things consistent. For example, if you’re baking cookies, making sure each batch comes out tasting just as delicious as the last one, every single time.
When you put them together, you get a method that helps you make processes smoother, faster, and more reliable.
At its core, Lean Six Sigma is about continuous improvement. It encourages teams to:
- Identify what adds value to the customer.
- Eliminate what doesn’t (waste).
- Standardise high-performing processes.
- Use data and statistical tools to drive decision-making.
The combination of Lean and Six Sigma ensures that improvements are both efficient and consistent.
What is Waste in Lean Six Sigma?
One of the foundational principles of LSS is recognising and removing “waste.” Now you might wonder: What is waste?
In Lean terminology, there are 8 types of waste, often remembered with the acronym DOWNTIME. These tasks are called waste because they somehow take up your productive time and don’t add value to the customer.
Think about all the work you do in a day while you go through this list and see how much of your day is filled with work that is unproductive or “waste”:
- Defects – Errors in a task that require rework.
(E.g. faulty design that has to be redesigned as per the creative brief) - Overproduction – Producing more than what is needed.
(E.g. writing more than one contract “just in case”) - Waiting – Time lost due to delays or waiting around.
(E.g. waiting for an email or for a co-worker to hand you over a project) - Non-utilised talent – Skills or knowledge that’s not used or leveraged.
(E.g. Spending more time of the day doing admin work rather than strategising for improvement) - Transportation – Unnecessary movement of materials.
(E.g. Sending files back and forth via email when a shared cloud document would suffice) - Inventory – Excess products or materials.
(E.g. Purchasing software licenses for the entire team when only a few members need them - Motion – Unnecessary movement by people.
(E.g. Constantly switching between multiple software applications to complete a single task) - Extra-processing – More work or higher quality than required.
(E.g. Multiple layers of approval for routine, low-risk decisions)
By identifying these areas of waste, you can systematically improve your productivity and profitability.
Lean Six Sigma Methodologies
LSS relies on structured, proven problem-solving frameworks. The two main methodologies of Lean Six Sigma are:
- DMAIC – The Process Improvement Formula: Used for improving existing processes.
DMAIC stands for Define, Measure, Analyse, Improve, and Control. This methodology provides a structured approach to improving existing processes that aren’t performing as well as they should.
When to use DMAIC:
- When you have an existing process with known problems
- When you need to reduce defects or variation in current operations
- When you want to optimise something that’s already working but could work better
Example: A hospital uses DMAIC to reduce patient wait times. After defining the problem and measuring delays, they analyse the root causes (staff allocation), implement changes, and monitor results to sustain improvements.
2. DMADV – The New Creation Formula: Used when creating new processes or products.
DMADV stands for Define, Measure, Analyse, Design, and Verify. This methodology is used for creating entirely new processes, products, or services from scratch.
When to use DMADV:
- When you need to develop a completely new process or product
- When an existing process is fundamentally broken and needs replacement
- When customer needs have changed dramatically
Example: A coffee shop chain wanted to create a self-service ordering kiosk to reduce wait times and improve order accuracy
They defined their requirement of reducing wait time and improving accuracy, measured exactly what the customers wanted through surveys, analysed different apps and payment systems to implement, designed the solution, and verified the end result in 1 branch before rolling it out in the rest of the branches.
Apart from these two frameworks, Lean also relies on the 5Ss, Kanban, Value Stream Mapping, Heijunka Box, Ishikawa Fishbone Diagrams, and more.
Understanding Lean Six Sigma Belts
Just like Six Sigma, LSS follows a belt certification system, each level signifying a different level of expertise:
- White Belt: Introductory understanding of LSS concepts.
- Yellow Belt: Supports projects and understands basic tools.
- Green Belt: Leads smaller projects or works under Black Belts.
- Black Belt: Expert in LSS methodologies; leads projects and mentors teams.
- Master Black Belt: Strategic leader guiding enterprise-wide initiatives.
Whether you’re new or experienced, there’s a belt level to suit your career path. To learn more about the belts and how you can become a certified Lean Six Sigma professional, contact your nearest training institute offering this course.
Lean Six Sigma vs. Six Sigma: What’s the Difference?
While both aim to improve processes and reduce defects, there are key differences:
LSS adds more agility and speed to the traditional Six Sigma model, making it more adaptable to fast-changing industries.
Benefits of Lean Six Sigma
LSS delivers tangible benefits to both individuals and organisations:
For Professionals:
- Enhanced problem-solving and analytical skills
- Career advancement opportunities
- Increased confidence and influence at work
- Global recognition through certification
For Businesses:
- Reduced operational costs
- Improved quality and consistency
- Higher customer satisfaction
- Increased employee engagement and performance
Case Studies: Six Sigma and Lean Six Sigma in Action
- General Electric (GE): GE was one of the early adopters of Six Sigma, saving over $10 billion in the first five years of implementation. The company used LSS across divisions to reduce defects and improve manufacturing processes.
- Amazon: Amazon has used Lean Six Sigma principles to enhance its logistics and customer service. From minimising packaging waste to speeding up delivery times, LSS has helped the company scale efficiently while maintaining high quality.
Tips for Applying Lean Six Sigma in Your Career or Business
- 💡Start small: Identify one process or task you can improve.
- 💡Use data: Don’t rely on guesswork—measure performance.
- 💡Involve your team: Continuous improvement thrives on collaboration.
- 💡Get certified: Build credibility and gain practical tools through a structured course.
Take the First Step with WingsWay
More than a buzzword, Lean Six Sigma is a must-have skill for modern professionals. With its blend of analytical rigour and practical efficiency, LSS empowers individuals and organisations to unlock their full potential.
So, the question is: Are you ready to lead smarter, faster, and better?
At WingsWay Training Institute, our Lean Six Sigma courses are CPD-accredited and globally recognised. Whether you’re starting out or ready to advance to Black Belt, our experienced trainers and real-world projects will help you apply what you learn with impact.
Transform your mindset. Elevate your skills. Lead change.
Explore our Lean Six Sigma course today and start your journey towards operational excellence.